Unlocking DPMO: Your Guide To Process Excellence
In the relentless pursuit of operational perfection, businesses constantly seek robust metrics to gauge their performance and identify areas for improvement. One such pivotal metric, deeply rooted in the principles of Six Sigma, is DPMO. Understanding the DPMO meaning is not merely about grasping an acronym; it's about unlocking a powerful lens through which to view, analyze, and elevate the quality and efficiency of any process. This comprehensive guide will demystify DPMO, exploring its definition, calculation, benefits, and its indispensable role in driving continuous improvement initiatives across various industries.
Whether you're a seasoned quality professional, a business leader striving for operational excellence, or simply curious about how top-tier organizations measure and minimize errors, delving into DPMO will provide invaluable insights. We will explore how this metric standardizes performance measurement, enables meaningful comparisons, and ultimately helps build a culture of precision and customer satisfaction. Join us as we uncover the power of Defects Per Million Opportunities.
Table of Contents
- What is DPMO Meaning?
- The Genesis of DPMO: Six Sigma and Quality Management
- Deciphering the 'Defect': A Crucial First Step
- The DPMO Formula: Breaking Down the Calculation
- Why DPMO Matters: Benefits for Business
- DPMO and Six Sigma: A Powerful Partnership
- Interpreting DPMO Values: What the Numbers Tell You
- Practical Application: Implementing DPMO in Your Operations
What is DPMO Meaning?
At its core, DPMO stands for Defects Per Million Opportunities. It is a fundamental metric in quality management, particularly within the Lean Six Sigma framework, designed to quantify the number of defects in a process or product per one million opportunities for those defects to occur. Sometimes, it is also referred to as Nonconformities Per Million Opportunities (NPMO), with both terms essentially serving the same purpose of measuring process performance.
- 22 Shades Nail Studio Reviews
- Chris Brown Kids
- Hard Fought Hallelujah Lyrics
- Quagmire Family Guy
- Weezer Meme
The essence of DPMO lies in its ability to provide a standardized, quantifiable measure of quality. It's not just about counting how many flaws you find; it's about understanding the rate at which these flaws appear relative to the total chances for them to happen. This ratio is then scaled up to a million to make it easier to compare processes, especially those with very low defect rates. The lower the value of DPMO, the better the process performance, as it directly correlates with a reduced probability of defects.
Imagine a manufacturing line producing thousands of units daily. Each unit might have multiple potential points where a defect could occur – perhaps a faulty component, an incorrect assembly step, or a cosmetic blemish. DPMO allows organizations to aggregate all these potential defect points and present a single, comparable figure that reflects the overall quality output. This metric is crucial for process improvement efforts because it offers clear, actionable insights into the efficiency and effectiveness of a process, highlighting where attention is most needed to minimize errors and enhance overall quality.
The Genesis of DPMO: Six Sigma and Quality Management
To truly appreciate the DPMO meaning, one must understand its roots in Six Sigma. Six Sigma is a data-driven methodology used to eliminate defects in any process, from manufacturing to transactional and service-related processes. Its ultimate goal is to achieve near-perfection, striving for a level of quality where only 3.4 defects occur per million opportunities. This aspirational target is precisely where DPMO becomes indispensable.
Before the advent of metrics like DPMO, quality measurement often relied on simpler percentages, such as "defective units per hundred" or "yield." While useful, these metrics struggled to adequately represent processes with extremely high quality levels. For instance, a process with a 99.9% yield might sound impressive, but when scaled to a million opportunities, it still means 1,000 defects. Six Sigma, with its ambitious 3.4 DPMO target, necessitated a metric that could articulate such minute defect rates effectively and allow for precise comparisons across vastly different operations.
DPMO standardizes the number of defects at the opportunity level, making it incredibly useful for comparing processes with varying complexities and scales. Whether you're comparing the quality of software code, the accuracy of medical diagnoses, or the efficiency of a customer service call center, DPMO provides a common benchmark. This standardization is a cornerstone of effective quality management, allowing organizations to establish a universal language for performance evaluation and drive consistent improvements.
Deciphering the 'Defect': A Crucial First Step
Before any calculation of DPMO can commence, the single most crucial factor is the clear and unambiguous definition of what constitutes a 'defect' within the specific context of your process or product. A defect, in the simplest terms, is a flaw or discrepancy in a process or object that fails to meet a specified requirement or standard. Without a precise definition, your DPMO calculation will be meaningless and inconsistent.
Consider a simple example: a printed brochure. What could be a defect?
- Misspelled word
- Incorrect color reproduction
- Smudged ink
- Missing page
- Incorrect folding
The definition of a defect must be specific, measurable, achievable, relevant, and time-bound (SMART). It should leave no room for subjective interpretation. This meticulous approach to defining defects is foundational to the accuracy and utility of the DPMO metric. It directly impacts the trustworthiness of your data and, consequently, the effectiveness of your process improvement initiatives. Without this foundational step, the power of DPMO meaning remains untapped.
The DPMO Formula: Breaking Down the Calculation
Understanding the DPMO meaning is incomplete without knowing how to calculate it. The formula for Defects Per Million Opportunities is straightforward, yet requires careful consideration of its components:
DPMO = (Number of Defects / (Number of Units x Opportunities Per Unit)) x 1,000,000
Let's break down each element of this formula to ensure a clear understanding:
Identifying Units and Opportunities
The 'Number of Units' refers to the total quantity of items, services, or transactions produced or processed during the period under observation. For example, if you're evaluating a manufacturing line, the units might be the number of products assembled. If it's a customer service process, the units could be the number of customer interactions handled.
'Opportunities Per Unit' is where the concept of "per million opportunities" truly comes into play. This represents the total number of potential points within a single unit where a defect could occur. It's crucial to identify all possible areas where a flaw might arise. For instance, if you are assembling a smartphone, each phone (unit) might have 50 potential defect opportunities, such as:
- Screen installation (1 opportunity)
- Battery connection (1 opportunity)
- Camera module alignment (1 opportunity)
- Speaker functionality (1 opportunity)
- Software installation (1 opportunity)
- Each of 4 screws tightened correctly (4 opportunities)
- Each of 4 buttons functioning (4 opportunities)
- Each of 2 ports working (2 opportunities)
- And so on...
Counting Defects Accurately
The 'Number of Defects' is the total count of flaws or nonconformities observed across all the units and their respective opportunities. It's important to note that one unit can have multiple defects. For example, a single smartphone might have a misaligned camera AND a non-functional speaker. In this case, that one unit contributes two defects to the total count.
Let's illustrate with a simple example:
Suppose a company manufactures 100 units of a product.
Each unit has 5 potential defect opportunities (e.g., 5 critical assembly points).
During inspection, a total of 10 defects are found across all 100 units.
Number of Units = 100
Opportunities Per Unit = 5
Number of Defects = 10
DPMO = (10 / (100 x 5)) x 1,000,000
DPMO = (10 / 500) x 1,000,000
DPMO = 0.02 x 1,000,000
DPMO = 20,000
This means for every million opportunities for a defect to occur in this process, 20,000 defects are expected. This calculation provides a clear, standardized measure of the process's current quality level, making the DPMO meaning tangible and actionable.
Why DPMO Matters: Benefits for Business
The adoption and consistent application of DPMO offer a myriad of benefits that extend far beyond mere quality measurement. It serves as a powerful catalyst for operational excellence, driving improvements that impact the bottom line and customer satisfaction.
Standardized Performance Measurement
One of the most significant advantages of DPMO is its ability to standardize the measurement of process performance. By calculating DPMO, companies can establish a common benchmark to evaluate the quality and efficiency of their processes, regardless of their scale or complexity. This allows for:
- Cross-Process Comparison: You can compare the quality performance of a manufacturing line with that of a customer service department, even though their operations are vastly different. DPMO provides an "apples-to-apples" comparison.
- Benchmarking: It enables organizations to benchmark their performance against industry best practices or internal targets, fostering a culture of continuous improvement.
- Consistent Reporting: It provides a consistent and easily understandable metric for all levels of the organization, from front-line employees to senior management.
Driving Continuous Improvement
DPMO is not just a reporting tool; it's a diagnostic one. It provides actionable insights that help minimize errors and enhance efficiency. By quantifying how many defects or mistakes occur per million chances for them to happen, DPMO helps pinpoint problem areas. The lower the DPMO value, the better, indicating a higher level of process control and fewer defects. This directly supports Lean Six Sigma and continuous improvement initiatives by:
- Identifying Bottlenecks: High DPMO values in specific process steps highlight areas that require immediate attention and root cause analysis.
- Measuring Impact: It allows organizations to quantitatively measure the impact of process changes and improvement projects. If a new procedure is implemented, a reduction in DPMO confirms its effectiveness.
- Fostering Accountability: By setting DPMO targets, teams become more accountable for the quality of their output, driving a proactive approach to defect prevention.
Enhancing Customer Trust and Satisfaction
Ultimately, defects impact the customer experience. A product with flaws, a service with errors, or a process that consistently fails to meet expectations will erode customer trust and lead to dissatisfaction. By diligently working to reduce DPMO, businesses directly enhance their ability to deliver high-quality products and services consistently.
- Improved Product/Service Quality: Lower DPMO means fewer defects reaching the customer, leading to higher perceived quality and reliability.
- Reduced Rework and Waste: Fewer defects translate to less rework, lower warranty costs, and reduced waste, directly impacting profitability.
- Stronger Brand Reputation: A reputation for quality and reliability builds customer loyalty and attracts new business through positive word-of-mouth.
DPMO and Six Sigma: A Powerful Partnership
The relationship between DPMO and Six Sigma is symbiotic. DPMO is the primary metric used to define and measure the "sigma level" of a process. The sigma level is a statistical representation of how well a process is performing, indicating how many standard deviations fit between the process mean and the nearest specification limit. A higher sigma level signifies a better, more controlled process with fewer defects.
Once you have calculated the DPMO for a process, you can use a Six Sigma conversion table to find its corresponding sigma level. For instance, a DPMO of 3.4 is the benchmark for a Six Sigma level process, meaning only 3.4 defects per million opportunities. This is considered near perfection.
Consider the example from the data: if you look for your DPMO of 750,000, it will fall between a sigma level of 0.80 and 0.85. Using your eyeball, you might extrapolate between those values and get 0.83, which is what the calculator above gave you. This demonstrates how DPMO directly translates into a quantifiable sigma level, providing a clear picture of process capability.
This powerful partnership allows organizations to:
- Set Ambitious Targets: By aiming for higher sigma levels, companies set clear, data-driven goals for quality improvement.
- Track Progress: DPMO allows for continuous monitoring of progress towards these sigma level targets.
- Prioritize Improvement Projects: Processes with lower sigma levels (and thus higher DPMO) are identified as prime candidates for Six Sigma projects.
Interpreting DPMO Values: What the Numbers Tell You
Understanding the numerical value of DPMO is key to leveraging its power. As established, a lower DPMO is always better. But what do specific values signify?
The most famous DPMO value is 3.4. What does a DPMO of 3.4 mean? It means that for every one million opportunities for a defect to occur, only 3.4 defects are expected. This figure represents the gold standard of Six Sigma quality, indicating an incredibly robust and stable process with minimal variation. Achieving 3.4 DPMO signifies an accuracy (yield) level of 99.99966%, which is virtually flawless.
Conversely, a very high DPMO value, such as 750,000, indicates a process that is highly prone to defects. This level of DPMO, as mentioned earlier, corresponds to a very low sigma level (around 0.83), signifying a process that is far from controlled and likely experiencing significant waste, rework, and customer dissatisfaction. Such a process would be a prime candidate for immediate and intensive improvement efforts.
Interpreting DPMO values also involves considering the context. A DPMO of 100 might be acceptable for a non-critical internal process, but catastrophic for a life-saving medical device. The acceptable DPMO threshold often depends on the industry, the criticality of the process, and customer expectations.
The accuracy (yield) can be calculated with the help of the DPMO table. This table typically maps DPMO values to corresponding sigma levels and yield percentages, providing a comprehensive view of process performance. By understanding these relationships, organizations can set realistic yet challenging quality targets and communicate their performance effectively across all levels.
Practical Application: Implementing DPMO in Your Operations
Implementing DPMO effectively within an organization requires a systematic approach and commitment to data integrity. When utilizing DPMO, there are several crucial factors to keep in mind to ensure its accurate and beneficial application:
- Clear Definition of 'Defect': As emphasized earlier, this is paramount. Before calculating DPMO, it's essential to clearly define what constitutes a 'defect' within the context of your process or product. This definition must be consistent and understood by everyone involved in data collection and analysis.
- Accurate Data Collection: The integrity of your DPMO calculation hinges on accurate data. Implement robust systems for counting units, identifying opportunities, and meticulously recording every defect. This might involve training personnel, using automated sensors, or establishing clear inspection protocols.
- Identifying All Opportunities: To determine DPMO, one should consider the quantity of units produced and the potential defect opportunities per unit. This requires a thorough process mapping exercise to identify every single point where a defect could potentially occur. Missing opportunities will artificially lower your DPMO, giving a misleadingly positive picture.
- Consistent Measurement Period: Choose a consistent period for data collection (e.g., daily, weekly, monthly) to ensure comparability of DPMO values over time.
- Training and Communication: Ensure that all relevant personnel, from operators to managers, understand the DPMO meaning, how it's calculated, and its importance to the organization's quality goals. Transparent communication of DPMO results can motivate teams and highlight areas for improvement.
- Integration with Improvement Methodologies: DPMO is most powerful when integrated with methodologies like Lean Six Sigma. Use high DPMO values as triggers for DMAIC (Define, Measure, Analyze, Improve, Control) projects to systematically eliminate root causes of defects.
- Regular Review and Action: Don't just calculate DPMO and file it away. Regularly review the trends, identify outliers, and use the insights to drive actionable improvements. The goal is not just to measure, but to improve.
By diligently following these principles, organizations can harness the full power of DPMO to assess and compare the performance of different processes within their operations. It provides a common language for quality, fosters a data-driven decision-making culture, and ultimately leads to superior products and services that build lasting customer trust.
Conclusion
In the dynamic landscape of modern business, the pursuit of quality and efficiency is not merely an option but a strategic imperative. Understanding the DPMO meaning is a critical step for any organization committed to achieving operational excellence. As we've explored, Defects Per Million Opportunities is far more than just a number; it's a powerful, standardized metric that provides unparalleled insight into process performance, identifies areas ripe for improvement, and serves as a direct link to customer satisfaction.
From its foundational role in Six Sigma to its practical application in defining defects, calculating performance, and driving continuous improvement, DPMO empowers businesses to quantify quality, compare diverse processes, and set ambitious targets for perfection. By meticulously defining defects, accurately collecting data, and consistently applying the DPMO formula, companies can transform their operations, reduce waste, enhance customer trust, and ultimately secure a competitive edge.
Embrace the power of DPMO to unlock the full potential of your processes. What are your thoughts on integrating DPMO into your quality management system? Share your experiences or questions in the comments below! If this article has shed light on the intricacies of DPMO, consider sharing it with your colleagues and exploring other related articles on process improvement and quality management on our site.
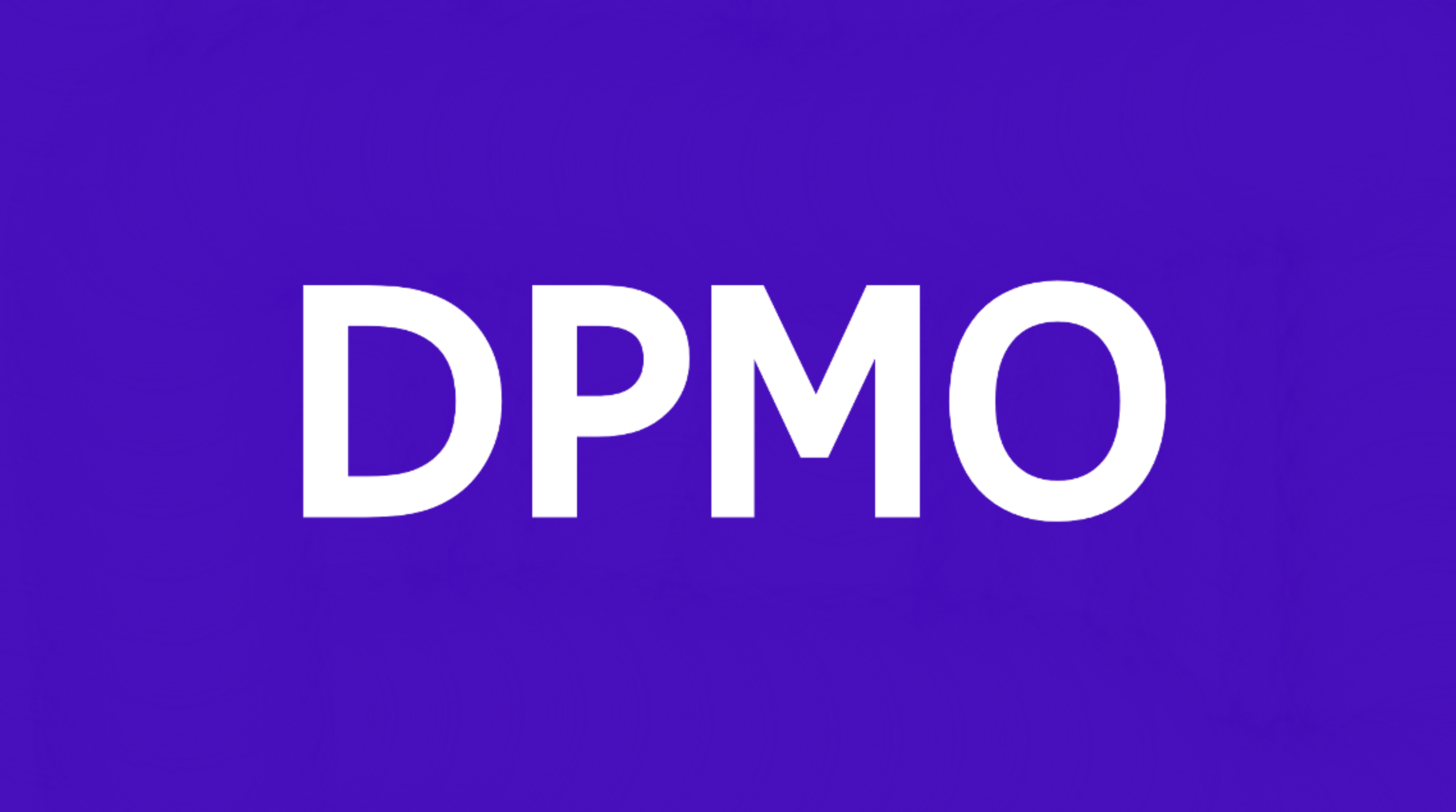
DPMO | Know Your Meme

What Is DPMO Slang? - Slangs Meaning

DPMO formula – ProdemyAsia.com